
The Function of an Inventory System and How to Optimize It in Business
Sovia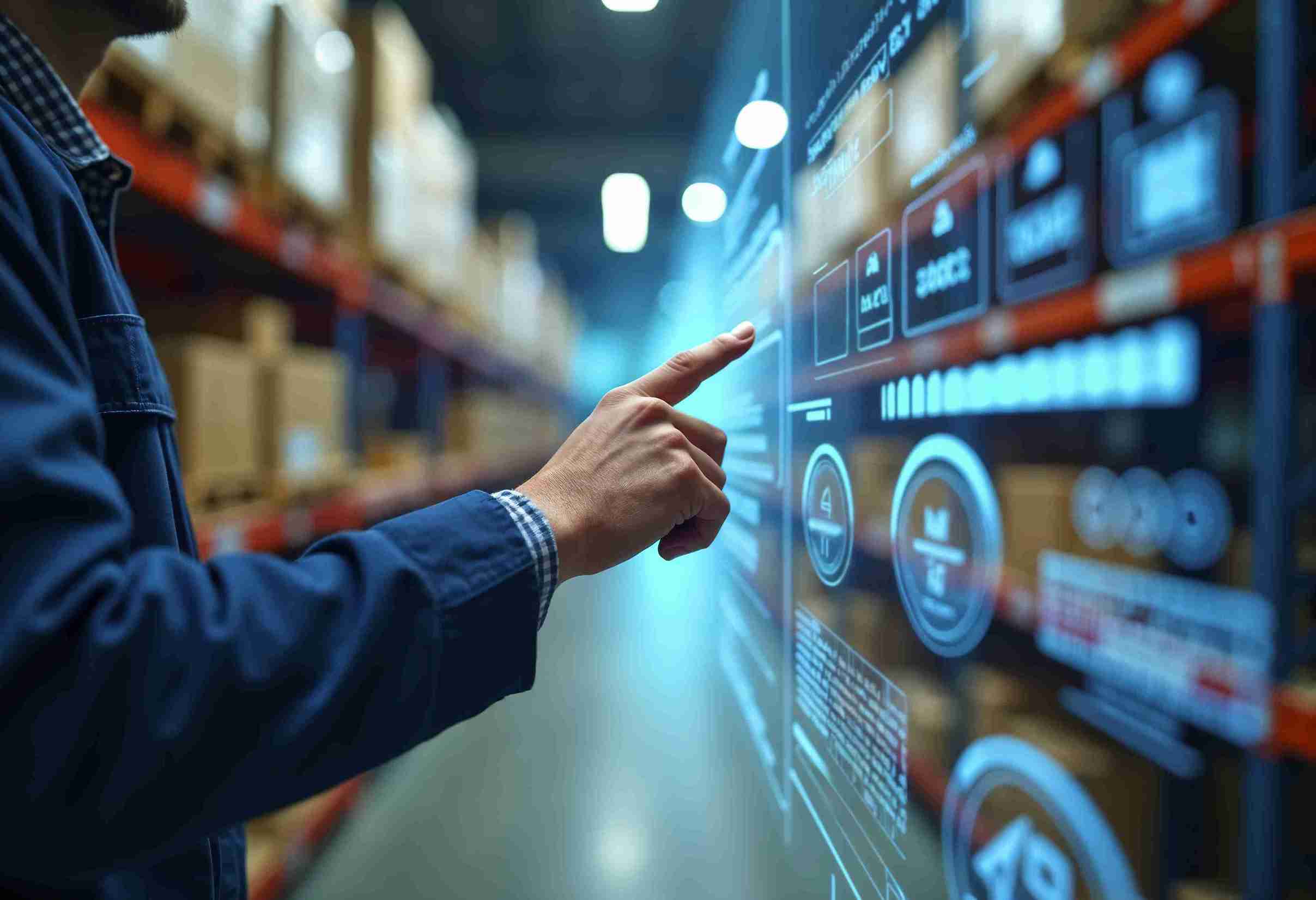
In the business world, inventory is a crucial element that affects operational efficiency and profitability. Without proper inventory management, companies risk facing excess or insufficient stock, which can be detrimental.
Therefore, managing inventory is not just about record-keeping but also a strategic approach to ensuring smooth operations and customer satisfaction.
In this article, we will discuss what inventory is, its functions, types, and how to manage it effectively.
Understanding Inventory
Inventory refers to a collection of goods or products stored by a company for future sales or use in production. Inventory includes raw materials, work-in-progress goods, and finished products ready for the market.
Proper inventory management is essential to maintain product availability while avoiding excessive stockpiling, which can lead to increased operational costs.
To prevent such issues, businesses need to implement efficient inventory management. Inventory management involves planning, procurement, organization, and control of goods or products owned by the company.
With the right strategy, businesses can balance supply and demand, ensuring they meet customer needs without facing stock shortages or surpluses.
One essential form of inventory in business is merchandise inventory. Merchandise inventory consists of trading goods owned by a company, whether obtained from suppliers or self-produced.
Effective merchandise inventory management ensures product availability in the market, allowing businesses to operate smoothly.
To measure stock management effectiveness, companies can use inventory turnover.
Inventory turnover is an indicator of how quickly a company can sell its inventory within a specific period.
The higher the inventory turnover, the more efficient the company is in managing stock and distributing products to customers.
By implementing the right inventory management strategies, businesses can optimize operations, reduce storage costs, and enhance customer satisfaction by ensuring product availability according to market demand.
Read more: How to Optimize Inventory Management for Your Business
The Functions of an Inventory System in Business
Inventory is not just a pile of goods in a warehouse; it is a valuable asset that ensures operational efficiency and keeps businesses competitive.
Here are some key functions of inventory in a company:
1. Ensuring Smooth Production and Sales
Well-managed inventory ensures that raw materials and ready-to-sell products are always available when needed.
This means production can proceed without interruptions, and sales remain consistent. Without adequate stock, you risk losing market momentum.
2. Reducing the Risk of Stock Shortages
Inventory plays a crucial role in preventing stockouts. If goods run out, production may be halted, and sales opportunities could be lost. With proper inventory management, this risk can be minimized.
3. Meeting Dynamic Market Demand
Markets are always changing, and sufficient inventory provides the flexibility to meet diverse customer needs.
Whether demand surges rapidly or customers need immediate products, inventory ensures that businesses can respond quickly.
4. Improving Financial Management
Efficient inventory management is not just about stock but also financial control.
By closely monitoring stock movement, businesses can better manage cash flow and optimize expenses. This directly contributes to increased profitability.
5. Maintaining Price Consistency in the Market
With adequate inventory, businesses can maintain stable product prices. Price fluctuations caused by supply and demand can be minimized, increasing customer trust and reinforcing the company’s reputation as a reliable product provider.
Types of Inventory
Source: freepik.com
Inventory plays a crucial role in business operations. Each type has a strategic function in the supply chain.
By understanding these differences, companies can manage stock more efficiently and minimize risks. Here are five common types of inventory in business:
1. Raw Materials
Raw materials are the foundation of the production process. Without them, producing the final product is impossible.
For example, the furniture industry requires high-quality wood, while the automotive industry relies on steel as a primary component.
2. Work-in-Progress (WIP) Inventory
This category includes products that are not yet fully completed. Work-in-progress inventory represents the transition phase from raw materials to finished goods.
For instance, automobile parts undergoing assembly before becoming a complete vehicle.
3. Finished Goods
Once production is complete, finished goods are ready for sale. This inventory is a key asset in meeting market demand.
A pair of shoes prepared for shipment to retail stores is an example of a finished product ready for consumers.
4. Safety Stock Inventory
Market uncertainties require companies to store backup stock. This inventory acts as a buffer during demand surges or supply chain disruptions.
For example, seasonal products stored in large quantities ahead of peak sales periods.
5. Transit Inventory
Goods being transported from one location to another fall under transit inventory. For example, products moving from a factory to a warehouse or from a warehouse to retail stores.
Proper management of this inventory can speed up distribution and prevent supply delays.
Effective Inventory Management Tips
Managing inventory is more than just organizing stock on shelves. If not handled properly, businesses can suffer profit losses, disrupted cash flow, and even customer loss. Here are some tips for effective inventory management:
1. Prioritize Inventory by Category
Not all inventory items have the same value. Categorize products based on importance and stock turnover.
Identify fast-moving items that must always be available and high-value products that move more slowly. This strategy helps avoid stock shortages or excessive storage costs.
2. Accurately Track Product Details
Each inventory item has crucial details like SKU, barcode, supplier, and lot number. Keeping accurate records allows you to track price changes due to external factors like scarcity or seasonal trends. Organized data also aids in more accurate restocking planning.
3. Conduct Regular Stock Audits
Many businesses conduct annual stock counts, but a more effective approach is to perform periodic checks.
High-turnover items should be counted more frequently, such as weekly or monthly. Regular audits ensure physical stock matches system records.
4. Evaluate Supplier Performance
Suppliers who frequently deliver late or provide substandard goods can disrupt business operations.
If issues persist, communicate with suppliers and find solutions. If necessary, switch to more reliable suppliers to maintain stock stability.
5. Apply the 80/20 Rule in Stock Management
Most business profits come from about 20% of products. Focus on these key products by closely monitoring their sales cycles.
Ensure stock availability and conduct regular sales analysis to optimize inventory turnover.
6. Standardize Goods Receiving Procedures
Employees handling stock must follow standard procedures when receiving, checking, and recording goods.
Without clear standards, minor discrepancies can lead to major differences in monthly reports. Verify and record all transactions accurately.
7. Analyze Sales Data in Depth
Tracking sales is more than just knowing total sold items. Understand trends, best-selling periods, seasonal products, or frequently bought product combinations.
By recognizing these patterns, you can create more effective inventory strategies.
8. Control Restocking Independently
Some vendors offer automatic restocking services, but this is not always the best option. Vendors focus on selling their products rather than your business's profitability.
Managing restocking independently ensures that incoming stock aligns with business needs.
9. Invest in Inventory Management Software
Small businesses may manage stock with spreadsheets, but as the business grows, manual tracking becomes time-consuming and error-prone.
Use inventory management software to automate stock tracking, analyze sales trends, and simplify bookkeeping.
10. Integrate Technology into Inventory Systems
Besides inventory management software, tools like barcode scanners and POS systems can enhance operational efficiency.
Ensure all systems are integrated so stock data remains accurate without manual input errors.
Read more: What is A Point of Sales (POS) and Its Benefits for Culinary Business
Conclusion
Inventory is one of the most important assets in a business. With proper management, businesses can operate more efficiently, avoid losses, and enhance customer satisfaction.
Understanding inventory types, functions, and effective management strategies will help businesses grow faster.
Want to manage your culinary business inventory more easily and efficiently?
Take advantage of ESB Core, an ERP system that enables business process automation, multi-branch stock management, and real-time performance monitoring.
Keep your business under control anytime, anywhere! Consult with the ESB Team now!
