
What is Safety Stock? Here
Briantama Afiq Ashari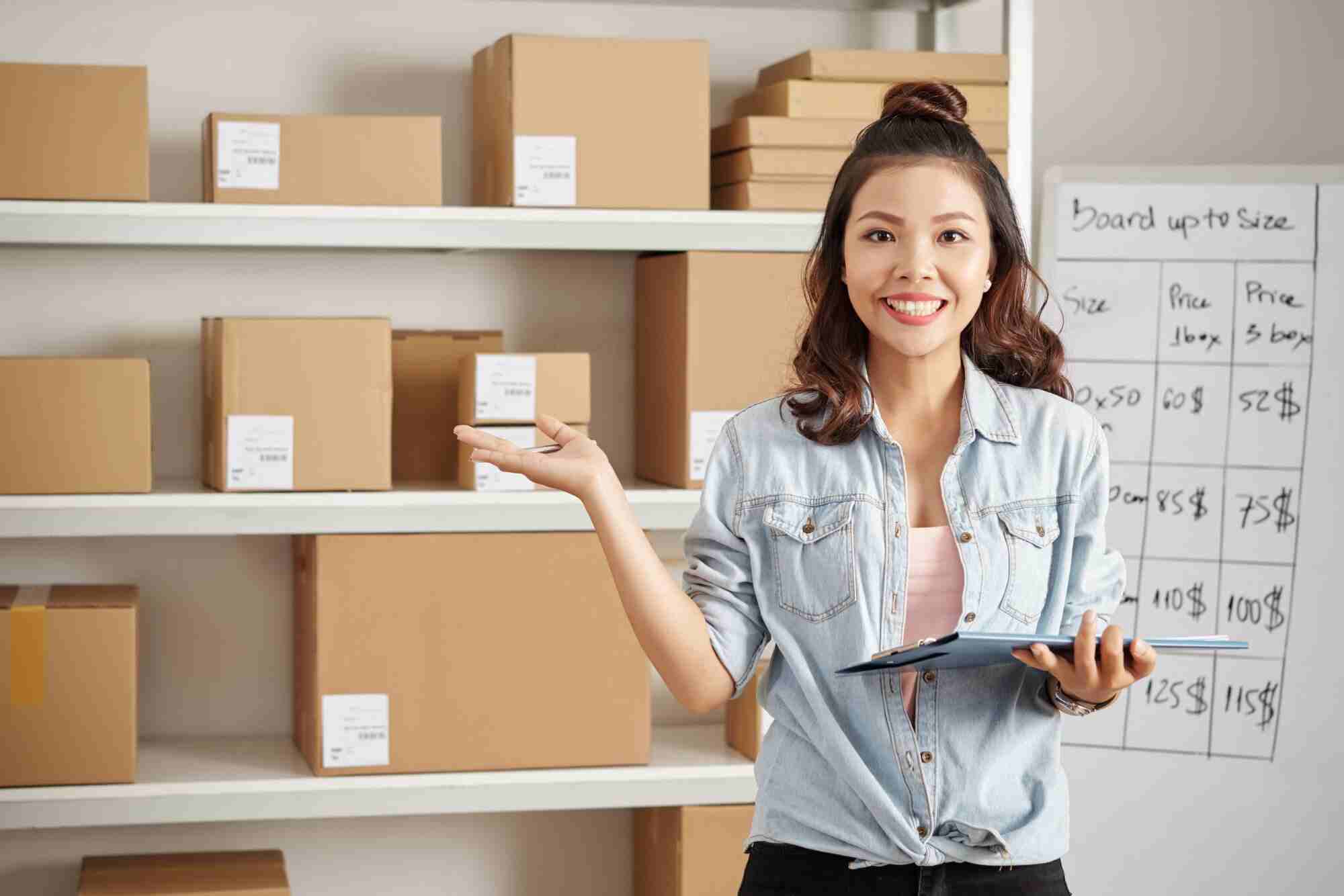
Have you ever experienced out of stock when demand was high? So, this problem often occurs if stock is not managed well.
Therefore, safety stock is a solution that can help businesses remain stable.
So, with this backup inventory, you can avoid shipping delays and losing customers.
However, how do you ensure there is always enough stock without going overboard?
You need to understand how to calculate safety stock, to be able to manage inventory more efficiently.
There are also formula safety stocks which can be used to determine the ideal amount of reserve stock.
Before discussing further, let's understand first what is safety stock and why this system is important for business!
Make sure you read this article to the end, OK! To get the benefits, take a look!
What is safety stock and why is it important?
Source: Freepik
Safety stock is reserve stock stored to anticipate unexpected demand or delays in delivery of goods.
In business, out of stock can cause a decrease in sales and loss of customers.
Without safety stock, businesses can have difficulty fulfilling orders when there is a spike in demand.
On the other hand, too much stock can also increase storage costs and the risk of goods expiring.
This is the reason why it is important to understand formula safety stock.
So, with the right calculations, you can ensure sufficient stock without burdening operational costs.
Read Also: Don't Take Notes Wrong! This is an example of a correct sales journal for your business
Benefits of Safety Stock for Business
Source: Freepik
Implementation safety stock This is essentially to keep stock safe.
Well, in business, this system has many benefits that can help operations remain smooth and avoid the risk of losing customers. Anything?
1. Increase Profits and Business Stability
The main goal of every business is to get maximum profits. Without safety stock, the risk of losing sales due to running out of goods is greater.
Just think about it if demand is high, but stock in the warehouse is empty.
Customers can switch to competitors, and this will certainly have a bad impact on your business.
2. Anticipate Demand Fluctuations
Customer demand is not always stable.
There are seasons when sales go up drastically, and there are also times when demand goes down. Well, safety stock is the solution to deal with this situation.
3. Makes it easier to plan production schedules
For businesses engaged in production, safety stock is very helpful in arranging production schedules.
This is important to avoid production downtime which could cause major losses.
4. Anticipate changes in market conditions
The market is always changing, raw material prices can rise suddenly, or demand for certain products can increase drastically.
Well, through safety stock, businesses can be more flexible in dealing with these changes.
When raw material prices rise, for example, you can still use reserve stock to fulfill orders without having to buy raw materials at high prices.
5. Determine the Right Inventory Amount
Maintaining stock balance is a big challenge in trading business. If there are too many, storage costs increase.
If it's too little, it's a risk stock out (out of stock) also increased. Well, main actor stock out among others:
- Demand fluctuations which are difficult to predict
- Inaccurate stock estimates
- Lead time (waiting time) suppliers vary.
Well, with formula safety stock, you can calculate the ideal stock amount to avoid this problem.
6. Provides more flexibility in stock management
Businesses that use the system safety stock have greater flexibility in managing inventory.
For example, if there is an error in demand forecasting, reserve stock can be used to overcome the problem.
7. Increase Customer Satisfaction with Safety Stock
Customers always want fast and easy-to-access availability of goods. If goods run out of stock, customers can be disappointed and move to competitors.
So, don't take it for granted!
Safety stock is a strategy that is operationally profitable, while also being effective in building long-term relationships with customers.
Do you understand the benefits? However, still confused about how to calculate safety stock correct? So, now, let's discuss how to determine the ideal amount of safety stock for your business!
Read Also: Get to know the ERP Program: Solutions for Business Efficiency and Digitalization
6 How to Calculate Safety Stock Accurately
Here's how to calculate safety stock accurately and correctly:
1. Basic Safety Stock Formula
The simplest way to calculate safety stock is to use the following basic formula:
Example:
- Maximum daily sales: 100 units
- Maximum lead time: 10 days
- Average daily sales: 80 units
- Average lead time: 7 days
Calculation:
So, the ideal reserve stock is 440 units.
2. Preparation of Standing Proposals
If you want a fixed reserve stock of a certain amount, use this method:
This method is suitable for businesses that have a stable demand pattern and do not want to carry out stock calculations periodically.
3. Heizer and Render Formulas
This method is used if the lead time from the supplier often changes. For this reason, here are the formulas and methods:
Here, WITH is the reliability factor. The higher the value WITH, the greater the reserve stock that must be prepared.
4. Time Based Calculations
This method uses past demand data to predict future stock needs.
Example: If in the last 3 months there has been an increase in demand of 20%, you can upgrade safety stock with the same amount to anticipate increasing demand.
5. Metode Greasley
This method combines standard deviation with average demand to get a more accurate reserve stock amount. The formula is as follows:
6. Economic Order Quantity (EOQ)
EOQ helps determine the ideal order quantity so that storage and ordering costs remain efficient. The formula is:
Well, this formula is suitable for businesses that want to optimize stock levels more effectively.
How to Optimize Safety Stock to Make Your Business More Efficient
Source: Freepik
After knowing how to calculate safety stock, the next step is to optimize it to make it more efficient.
Don't let reserve stock burden business operations. So, here are some ways you can do it:
1. Use a Digital System to Manage Stock
Manual stock management often causes recording errors. If you want to manage safety stock with more accuracy, use digital systems such as ERP.
With an ERP system, you can view stock directly real-time, set up automatic orders, and avoid stockouts without overstocking.
2. Monitor Demand Trends and Lead Time Regularly
Customer demand patterns may change. If it is not updated, reserve stock could be too little or too much.
Make sure you always check sales trends and lead times from suppliers regularly.
3. Adjust Safety Stock Based on Product Type
Not all products require the same amount of reserve stock.
Products with high demand or long lead times require more stock than products that are easy to obtain.
4. Ensure that the warehouse and distribution run efficiently
Have safety stock The ideal alone is not enough if the distribution system is deadlocked.
Make sure the goods are stored properly and ready to be sent at any time.
By implementing this method, stock can be more controlled and your business can run more smoothly without obstacles.
Conclusion
Now you know that safety stock is an important element in stock management that helps businesses keep running smoothly.
So, by understanding this article, you can avoid running out of stock or overstock.
To make stock management easier, use an ERP system such as ESB Core.
With its advanced features, you can control inventory, analyze finances, and increase operational efficiency more easily.
How? You understand, right? Now, it's time for you to use ESB Core! Don't let stock become a problem in your business!
Manage inventory more effectively with ESB Core right now! Ask the ESB Team now!
